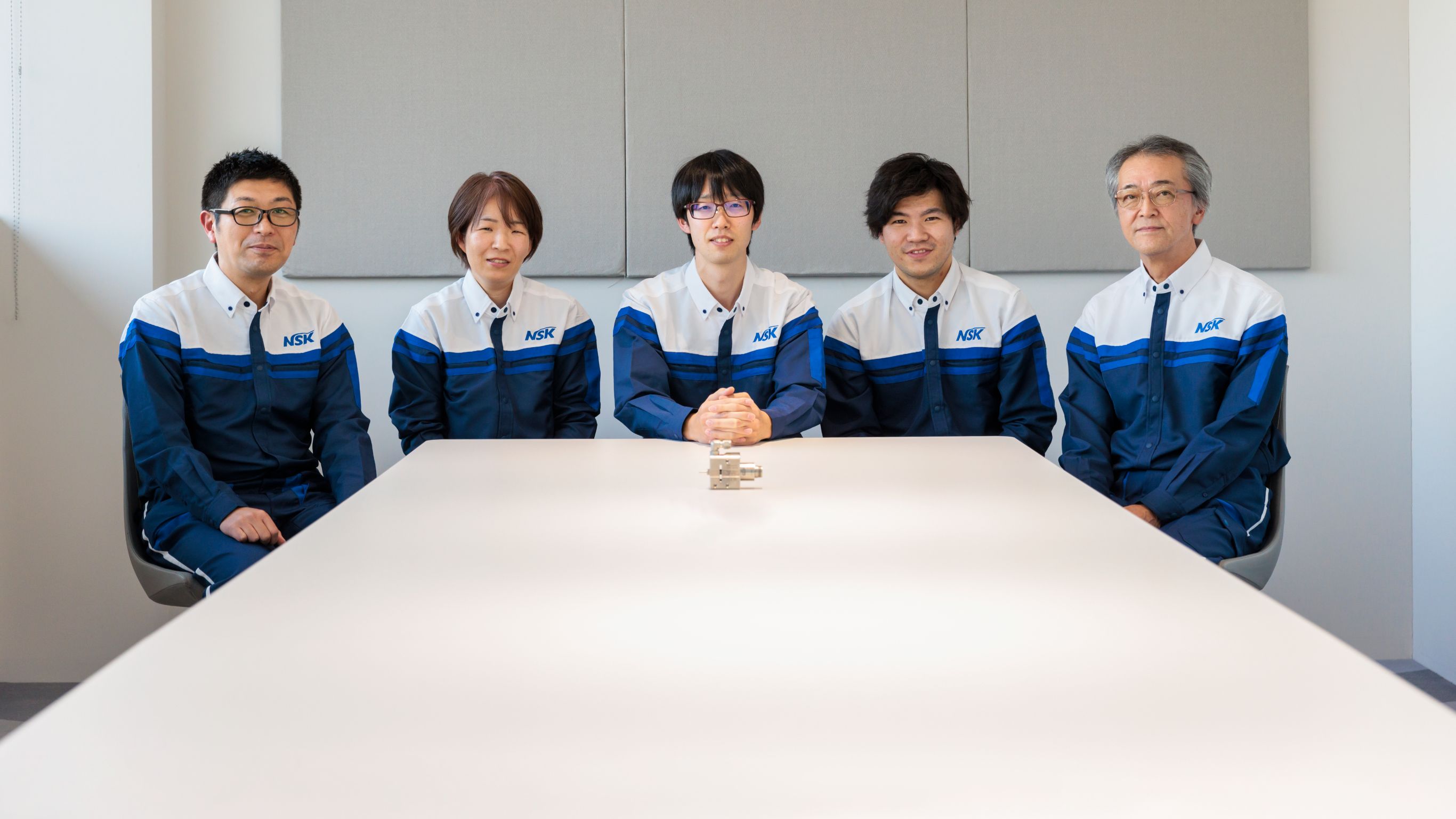
「一般産業用
クーラントスルースピンドル」
開発プロジェクト
INTRODUCTION
加工時間を
大幅に短縮する
新機軸の
スピンドル。
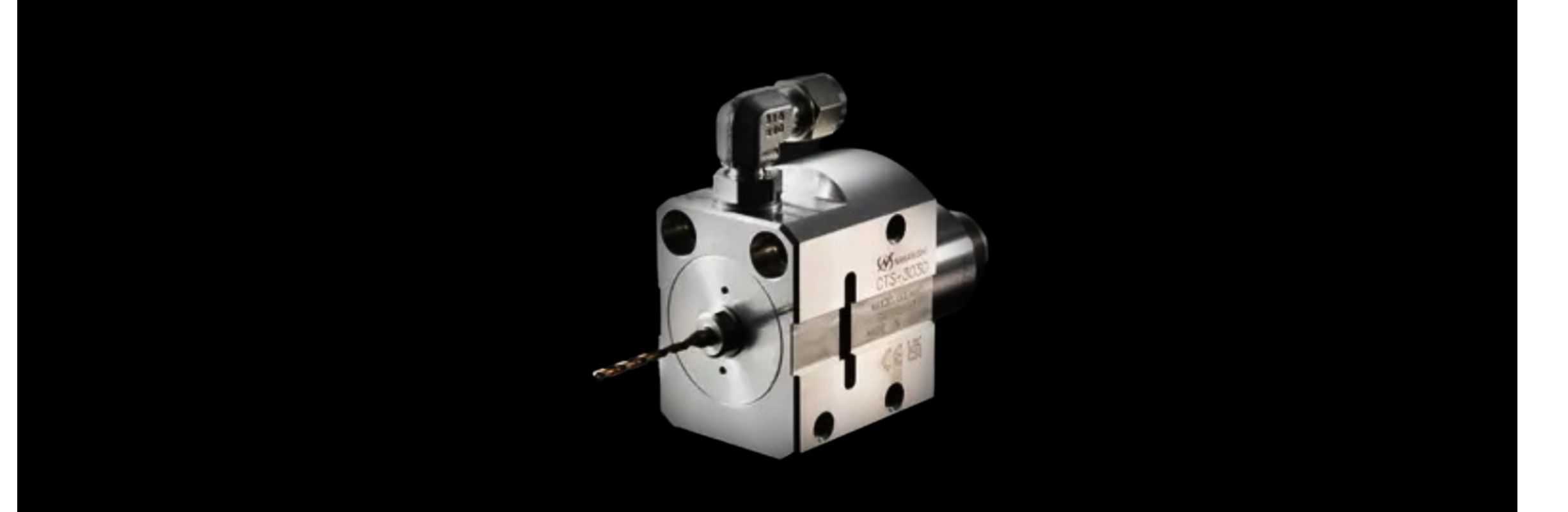
「高速回転」「高精度」「コンパクト」に特化した小型スピンドル。
精密加工の分野ではより速く、高精度の穴を開ける機器を常に求めています。
ナカニシは従来品のスピンドルを
さらに進化させるプロジェクトを始動。
市場の要望に応えるべく
最短上市に挑戦したメンバーたちの奮闘をご紹介します。
PROJECT
MEMBERS
-
機工設計部K.O.JOINED IN 2014
-
機工設計部M.Y.JOINED IN 1985
-
生産技術部T.T.JOINED IN 2017
-
サービス部Y.H.JOINED IN 2001
-
サービス部H.K.JOINED IN 2002
リーダーは心の中で
無理だ! と叫んだ。
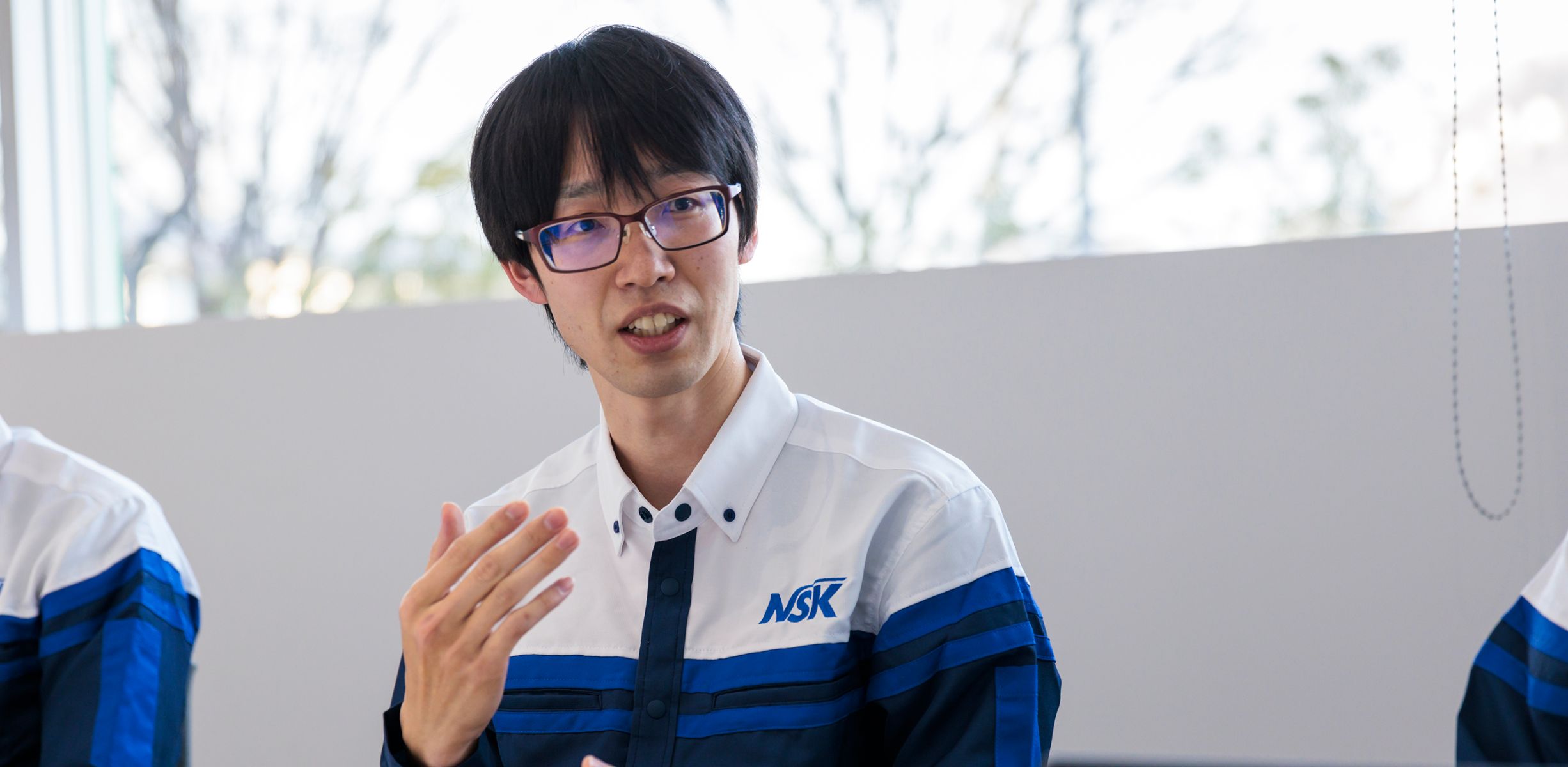
「6か月で完成させてほしい」
開発進捗の打ち合わせの場で耳を疑うような言葉が放たれた。プロジェクトリーダーのK.Oは、脳がバグって聞かなかったことにしようと思った。新規の要素技術が必要となる製品開発は通常では2年以上はかかる。どうする? いけるのか? 心の中で無理だ! と叫んだ。不安が込み上げてくる。自信のある返事ができないまま会議室を後にした。
様々な分野の精密加工において、穴をあける工程はどんな製品にでもある。需要は多く、国内外で様々なメーカーが機器を開発している。競争の激しい業界だが、ナカニシは小型モータスピンドルを生み出し、世界各地へ製品を供給している。モータスピンドルとは、モータとスピンドルを一つにした機器で、ドリル等の回転工具を取り付けて加工を行う。旋盤やロボット、専用機などの機械・装置に搭載し、ドリルでの穴あけ、エンドミルでの切削、超硬カッターやブラシでのバリ取りに使用される。性能が段違いなのは、「高速回転」「高精度」「コンパクト」だから。高速加工が可能なので加工時間を短縮できるのだ。しかし、いい製品はライバル企業から研究される。同性能の製品が出るのは時間の問題かもしれない。革新という名の伝統。それがナカニシにはある。もっと進化させよう。社長から号令がかかった。従来品のスピンドルの強化だ。それもパフォーマンスを圧倒的に上げる。ハードルは見えないぐらい高かった。
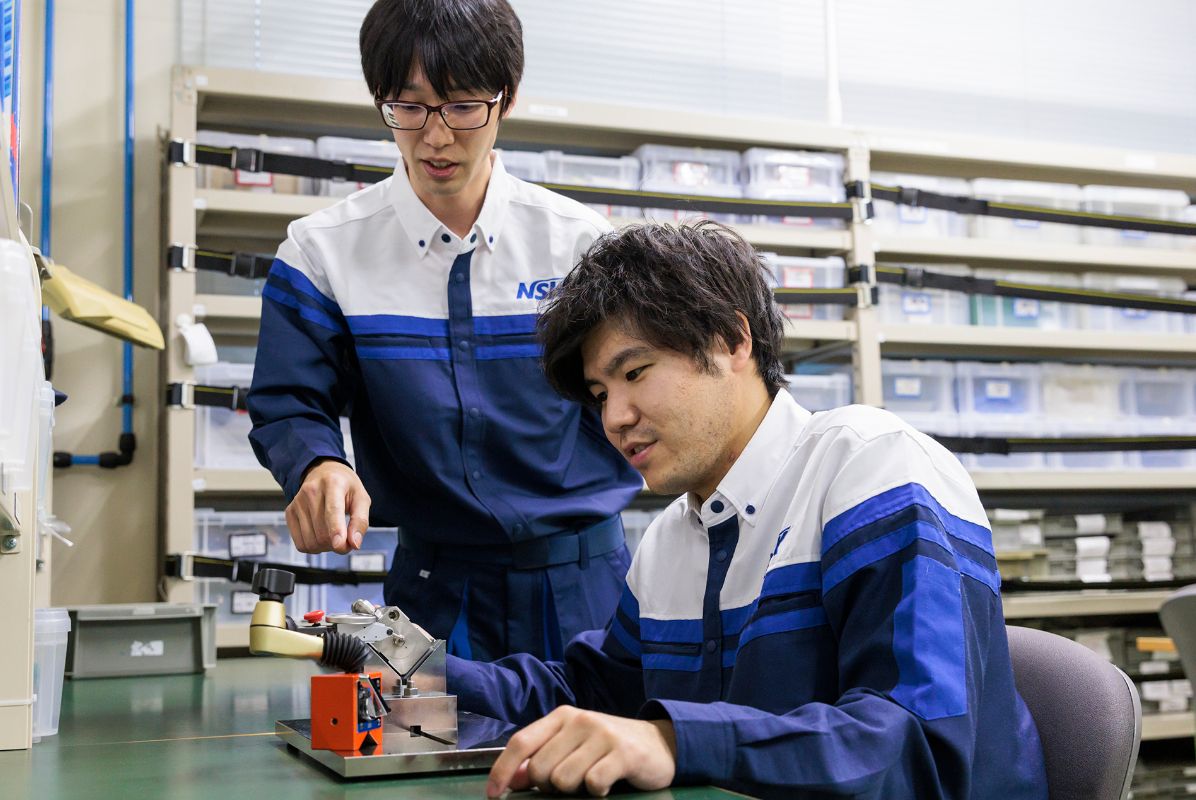
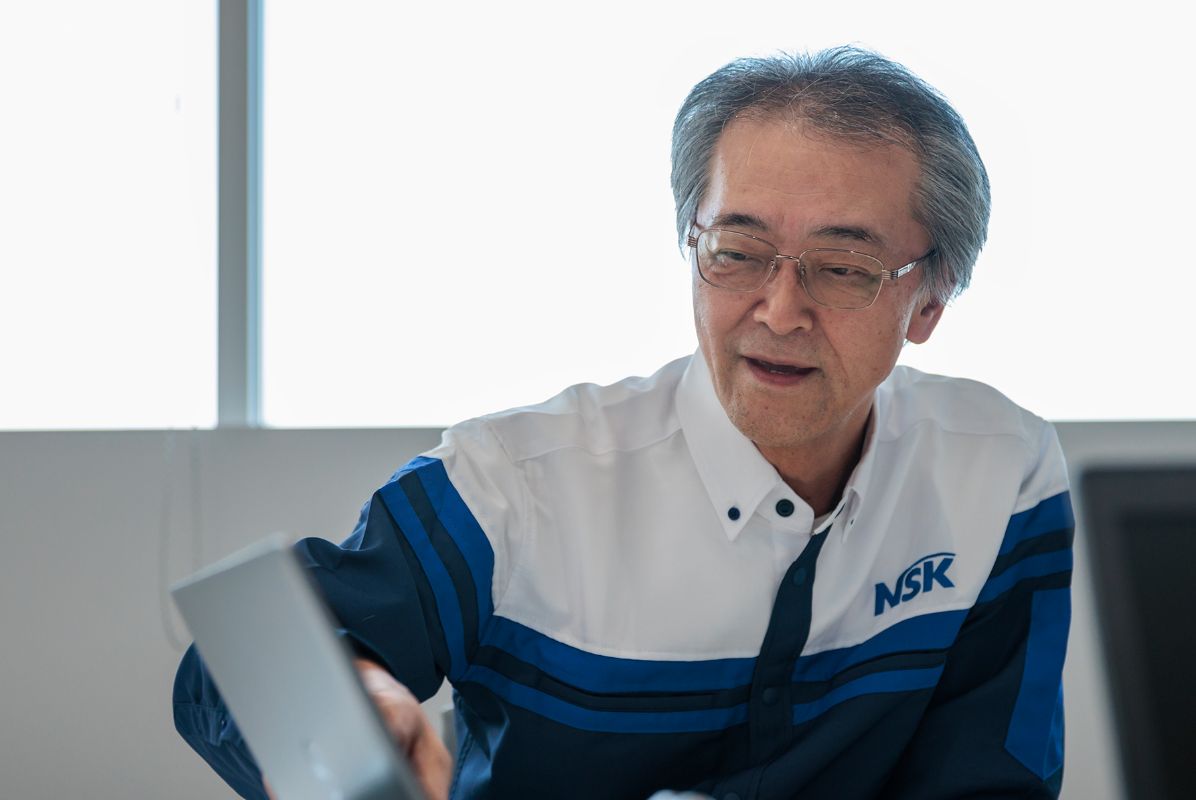
予定していた開発期間を大幅に縮められ、呆然としたK.Oだったが「できないとは言えないし、できると思ってくれたから無茶振りされた」と気分を切り替えた。予期せぬ問題が起きた時、チームには頼れる仲間がいる。M.Yだ。メンバーの中でも最年長で技術畑一筋でやってきた。彼に色々なことを教わったとK.Oは言う。早速相談を持ちかける。開発していた製品名は、クーラントスルースピンドル : CTS-3030。クーラントと聞いてピンときたらクルマに詳しい方だろう。クーラントとは、エンジンを冷却するための液体のことである。CTS-3030は、オイルホール付ドリル先端からクーラントを吐出させて深穴加工を行うスピンドルだ。ドリル先端からクーラントを吐出しながら削れば、切りくずを排出しやすくなり加工は速くなる。仕組みはわかるがM.Yの説明を聞いて驚いた。クーラント液を吐出する穴は2箇所ある。「一般的にドリル径が2mm以下の深穴加工は難しく最小で0.5mmのドリルがあるんですけど、ここから油を出すには圧力を上げないと出ない。タイヤの空気圧って0.2MPaぐらいでしょ? これは20MPaといってそれの100倍ぐらいの圧力を入れるんですよ」1MPaは約102トン。想像を絶する圧力が瞬時に発生するのだ。
若手とベテランが
切磋琢磨する
チーム
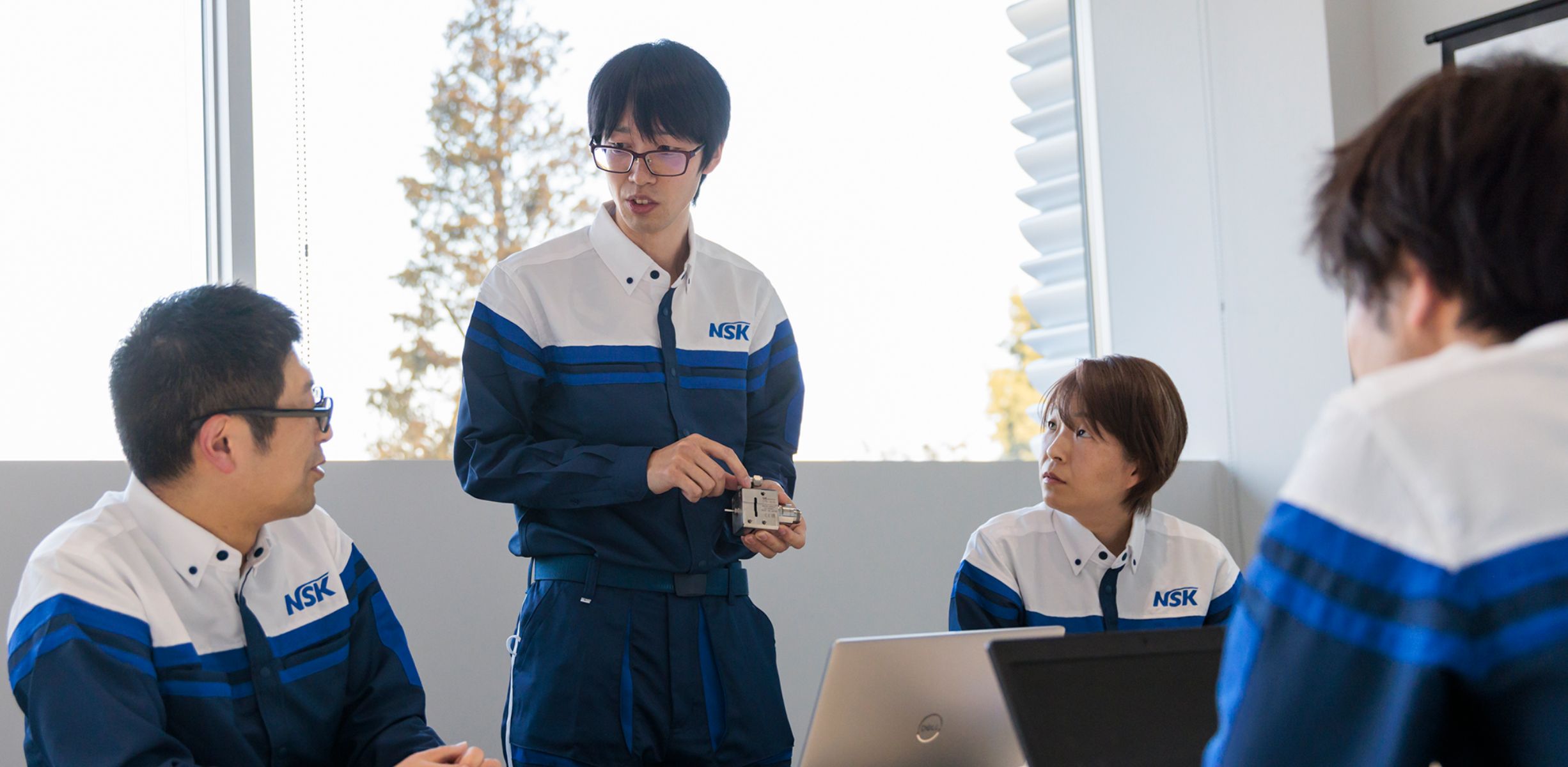
話はプロジェクトスタート時に遡る。従来品となるモータスピンドルは性能的には申し分なかった。ただ実際に現場で使っているお客様は、もっとこうしたい、こうはできないかと、改善を求めてくる。その声を営業がじっくり聞いて実現可能かどうかの計画を立てる。ライバル企業の情報も織り交ぜながら。製品化の目処がついたら営業部門、生産部門、そしてサービス部門のメンバーを集め、構造の改善とさらなる機能の強化を伝える。最初は設計がメインだ。K.OとM.Yは、設計検討に取り掛かる。ドリル加工時間の大幅短縮。それがお客様からの要望だ。確実にイメージができるまで何度も検討を重ねる。製品の輪郭が見えてきたところで図面の作成だ。ここでベテランのM.Yが各部門の要望と設計の要望がいい塩梅になるようにまとめるという。そのやり取りを見て若手は吸収するのだ。いいバランスでチームを組んでいる。加工時間を短くするには回転数を上げればいいというものではない。従来品で既に限界値まで攻めている。そこで、クーラント液を吐出しながら削れば速くなるというアイデアが出る。ただ、それを最適な構造でかたちにするのは容易ではなかった。
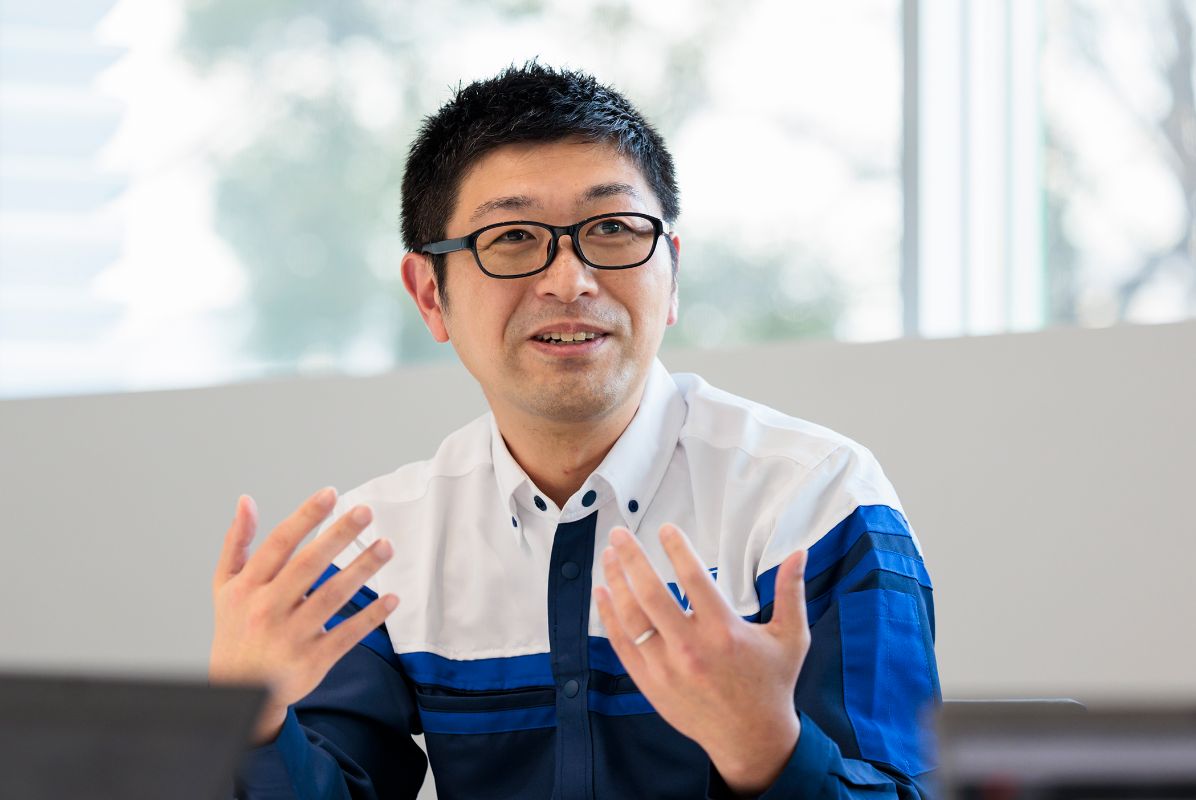
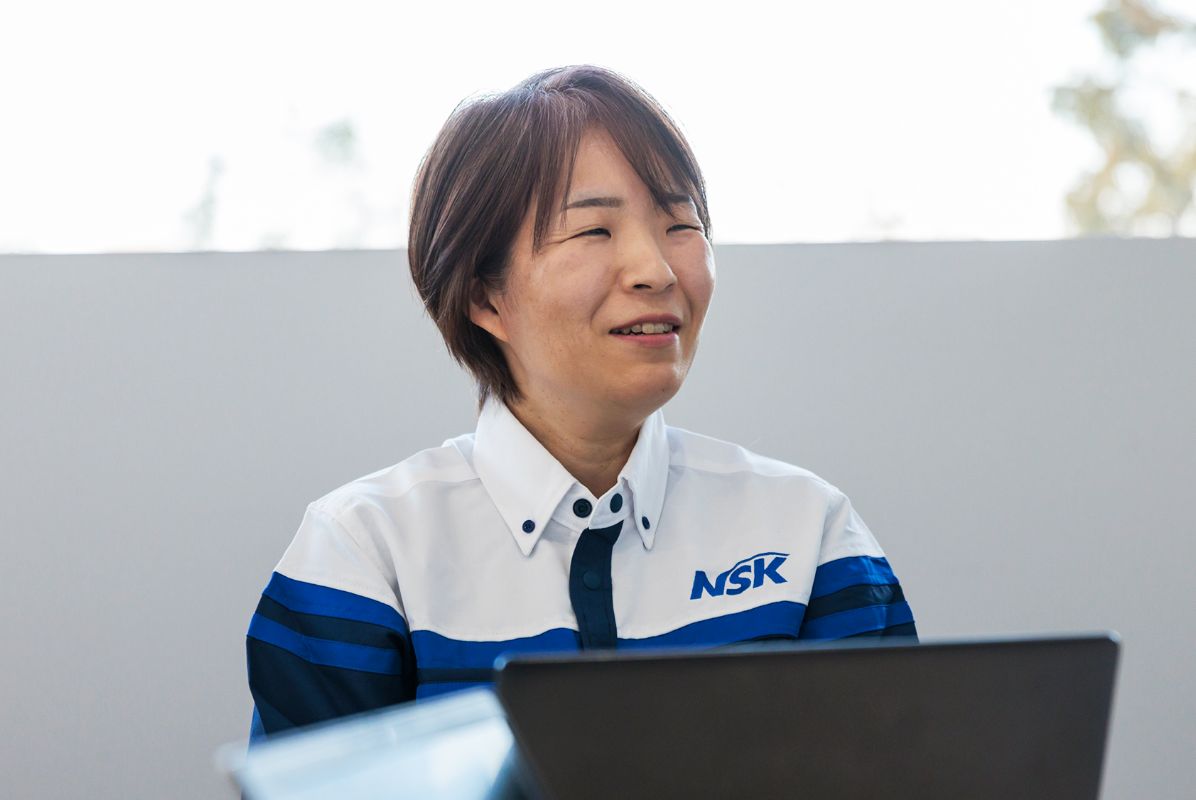
「この製品は構造自体が初めてなんです。世の中にないと言ってもいいぐらい。だから検証段階でかなり苦労しました」とK.O、M.Y、T.Tは口を揃えて言う。「検証は10回ほどやりました。すぐに原因はわからないのですが、わずかな数値の変化も見逃さずにチェックして詰めて、少しずつ直していきました」冒頭で述べたように、試作から上市までに与えられた時間は6か月。10回も検証していたらどう考えても間に合いそうにない。なぜ間に合ったのか。その理由はナカニシの体制にあった。設計室、実験エリア、加工工場がすべて同じ敷地内にあるからすぐ対処できるのだ。「ここだっていう箇所を特定して、改善したら、そのまま工場長のところへ行って直談判して最短でつくってくださいってお願いするんです。出来上がってきたら検証して、直して、またお願いしにいって、またつくってもらう。部品の修正で済むときは自分で機械加工して即日対処しました」それが納期に間に合った要因だと力説するK.Oの言葉にメンバー全員が頷く。
何か特別な方法があるわけではない。部門と部門の連携が見事にとれているのだ。風通しもいいのだろう。入社して間もない新人も他部署の人と遠慮なく意見を交わす。疑問がわいたり、こうしたいと思ったらまずは言ってみる。そこには意志がある。意志あるところに道は開けるとは社長の座右の銘だ。現場ではまさにその通りのことが起きていた。
従来品を
はるかに凌駕する
性能を実現。
この製品の特徴をまとめておくと、内部給油方式といってドリル内部よりクーラントを通して刃先より吐出させる。先端を見ると穴が二つあってそこから勢いよく吐出される油がドリルに絡みついて加工していく。加工性能を比較した実験動画を見ると違いは歴然だった。外部給油の従来製品と内部給油の新製品であるクーラントスルースピンドル。この2つでステンレス鋼のSUS304を同時に20mm貫通でφ1mmの穴あけをする。同じ時間でどれだけあけられるかを比べるのだ。加工時間1分25秒の間に従来品は1穴、新製品は15穴。結果として新製品は加工時間を大幅に短縮することが可能だということを証明した。3分16秒で穴数は364。切りくず排出性に優れ、工具の耐久性が向上。加工時間の短縮も実現するこの製品は革新どころか革命と言っても過言ではない。「ドリルを買う人が欲しいのはドリルではなく“穴”である」というアメリカの学者レビットの名言を思い出した。穴をあける。しかも短時間で多くの穴を。今のところこの製品と同等の製品はまだない。とんでもない製品をつくったのにそれを自慢することなく語ってくれるメンバーの姿はなんともカッコいい。
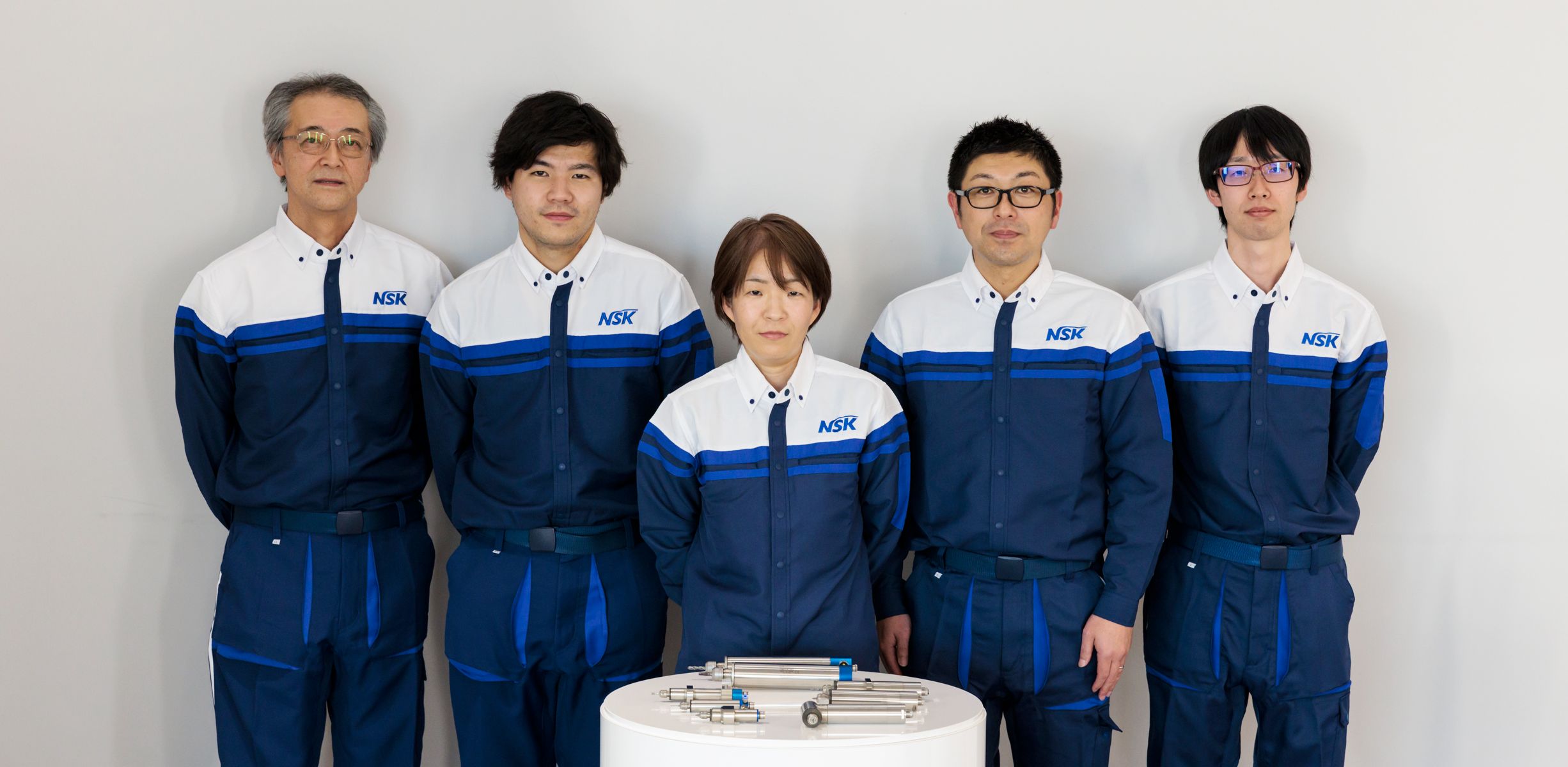
製品づくりは設計開発部門と生産部門がフォーカスされることが多いが、サービス部も重要な役割を担っている。製品の修理の手順を確立するのが仕事だ。分解着脱の仕方、交換する部品の単位、そういったものを決めていく。紅一点のY.Hはしっかりとした口調で教えてくれた。「プロジェクトが立ち上がって、こういった製品やりますよっていう話を聞いた時に、サービス要求報告書っていうのがあって、そこに既存の類似製品だったり、ここが修理しづらかったとか、ここをもうちょっと着脱しやすい構造にしてほしいとか、海外でも修理をやるので、接着剤だったり、シリコンだったりとか、副資材と言われるものは、海外で調達可能なものにして欲しいんだと、そういった要求を考えられる限り出します」いくら性能がよくても修理しづらい構造だと遠慮なく意見をぶつける。苦労して設計したことはわかっている。それでも改善点があれば伝える。それができるのは言いやすい環境だからだろう。以前品質保証部だったH.Kは、市場の苦情を受け止め、新しい機種で再発させないよう設計側にフィードバックしていた。縁の下の力持ち的な仕事であるが、彼のような人がナカニシの信頼を守っていることを忘れてはならない。全員で一つのチームなのだ。最短上市のプロジェクトは、このメンバーだから完遂できたのかもしれない。